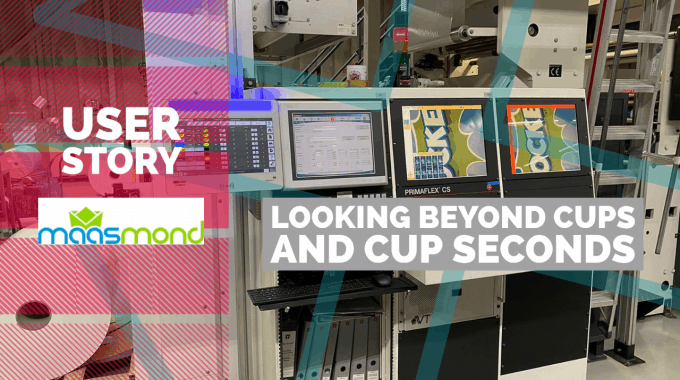
Maasmond BV realiseert nauwkeurige drukkleurnauwkeurigheid en -consistentie met Rheonics SRV- en RPS InkSight-systeem
BIJZONDERHEDEN
Aanvraag
Controle van de afdrukkwaliteit in flexodruk- en lamineereenheden.
Uitdaging
- Metingen van de viscositeit van de beker hebben niet de nauwkeurigheid om viscositeitgerelateerde afdrukproblemen in de pers eenvoudig op te lossen
- Handmatige kalibratie van viscositeitsmeters met een beker of een soort referentie is vervelend en inefficiënt
Oplossing
- De Rheonics De SRV-viscometer geeft ultrastabiele, herhaalbare en nauwkeurige metingen zonder dat herkalibratie nodig is
- Afgezien van een superieure controle van de afdrukkwaliteit, geeft de sensor veel inzicht in het gedrag van inkten, waardoor de kwaliteitscontrole naar een geheel nieuw niveau wordt getransformeerd.
- Met de RPS InkSight wordt een volledig automatische controle van de afdrukkwaliteit mogelijk gemaakt met extreme eenvoud en intuïtiviteit
GEBRUIKER
Bedrijf: Maasmond B.V
Locatie: Oostvoorne, Nederland
Contactpersoon: Bert Verweel, directeur & eigenaar
Over het bedrijf
Maasmond is een familiebedrijf (opgericht in 1969) met 50 jaar ervaring in het verwerken van papier en kunststof. Voor het omzetten van food en non-food verpakkingen en etiketten hebben wij een breed assortiment moderne smal- en breedband flexografische drukpersen (UV- en solventinkten), lamineren (water- en solventgebaseerde lijmen), snijden, stansen en perforeren machines. Maasmond produceert een breed assortiment hoogwaardige etiketten en flexibele verpakkingen die voldoen aan de hoogste normen voor voedselverpakkingen.
- Kunt u ons iets vertellen over uw bedrijf en zijn activiteiten? Hoe lang heeft uw bedrijf ervaring?
Reactie:
Maasmond is een familiebedrijf (opgericht in 1969) met 50 jaar ervaring in het verwerken van papier en kunststof. Voor het omzetten van food en non-food verpakkingen en etiketten hebben wij een breed assortiment moderne smal- en breedband flexografische drukpersen (UV- en solventinkten), lamineren (water- en solventgebaseerde lijmen), snijden, stansen en perforeren machines. Maasmond produceert een breed assortiment hoogwaardige etiketten en flexibele verpakkingen die voldoen aan de hoogste normen voor voedselverpakkingen.
- Hoe en wanneer bent u hiervan op de hoogte gekomen? Rheonics Afdrukoplossing (RPS)?
Reactie:
Ik was al een paar jaar op zoek naar vervangende viscositeitssensoren. In december 2017 kwam ik de website van Rheonics en wat mij meteen aansprak is de compactheid, robuustheid (bestand tegen hoge druk en schurende omgevingen) en nauwkeurigheid. In januari 2018 hebben we gedurende 2 dagen een aantal sensoren getest en we realiseerden ons meteen dat deze sensor fenomenaal is qua nauwkeurigheid en stabiliteit. Tijdens deze tests hebben we de hoeveelheid oplosmiddel gevarieerd en zelfs de invloed van retarder en versneller kon worden geregistreerd.
- Wat waren de belangrijkste uitdagingen waarmee u werd geconfronteerd en die u moest oplossen voordat u de RPS implementeerde?
Reactie:
Het nadeel van alle bestaande sensoren op de markt is dat ze altijd handmatig moeten worden gekalibreerd met een beker om een soort referentie te hebben. Vaak was bij het voorbereiden en aanpassen van een kleur de eerste vraag of de viscositeit correct is en of de sensor gekalibreerd is. Destijds varieerde de viscositeit van kleuren enorm (afwijkende waarden door niet-kalibreren), terwijl we nu met vaste waarden werken en dus veel sneller op kleur zijn. De dosering van oplosmiddelen was grof waardoor er een aanzienlijke viscositeitsafwijking ontstond.
- Heb je de uitdagingen kunnen oplossen?
Reactie:
De grootste uitdaging was wennen aan de mPa.s-unit, omdat we al decennia met Din Cup "Unity" werken. In het begin hebben we mPa.s geconverteerd naar Cupseconden, maar al snel besloten we dat dit onzin is, we hebben een sensor die werkt met de juiste eenheid met herhaalbare waarden, dus laten we die gebruiken. Sensor heeft ons ook veel extra kennis gegeven over het gedrag van inkten, durft zelfs meer te zeggen dan de inktleveranciers weten.
- Welke waarde heeft dit systeem opgeleverd in termen van printkwaliteit, productiviteit, besparingen en ROI?
Reactie:
Juist door de nauwkeurigheid van sensor en regeling wordt de viscositeit tijdens de productie uiterst nauwkeurig gehandhaafd, dE-waarden zijn constanter en nauwkeuriger geworden. Bijvoorbeeld: voor herhalingsopdrachten gebruiken we restinkt en doseren we de ontbrekende hoeveelheid inkt en kunnen we feitelijk dezelfde viscositeitswaarde behouden als de eerste keer dat de kleur werd gedrukt. Dit geeft veel vertrouwen bij de drukkers. Door de opgedane kennis en het gedrag van de inkt op de substraten waarop we printen, weten we welke waarden voor de viscositeit aangehouden moeten worden, wat veel tijd bespaart, restanten en verspilling (door handmatig testen en opstellingen).
Het toegenomen vertrouwen in controle over de printkwaliteit met de RPS heeft ons in staat gesteld om opdrachten met een hogere marge en hogere kwaliteit aan te nemen waarbij de merkeigenaren zeer strikte kleurspecificaties hanteren. We hebben een klant en een concurrent die ook folie levert, de dE2000-waarden liggen tussen de 4-5, de onze onder de 2. Onze verkoopprijs is hoger dan die van de concurrent en in dit geval is de prijs bepalend voor de kwaliteit. We streven altijd naar lage dE2000-waarden om het kwaliteitsniveau zo hoog mogelijk te houden en het de concurrentie moeilijk te maken. Het systeem heeft andere geavanceerde mogelijkheden, zoals de mogelijkheid om vervuiling / verstopping van de druklijn te detecteren. Deze intelligente functionaliteiten van RPS InkSight verlengen de levensduur van onze drukpersen met minimaal 2 jaar.
De systeemfunctionaliteiten strekken zich uit tot effectieve foutanalyse en probleemoplossing. Vorige week hebben we 'Ghosting' ervaren op onze printopdrachten - die meestal wordt veroorzaakt doordat de anilox niet constant voldoende inkt levert tijdens het printproces. Dit hebben we opgelost door in een aantal stappen ethylacetaat (zorgt ervoor dat de inkt goed oplost en sneller droogt) aan de inkt toe te voegen. De viscositeit daalde van 45 naar 32 mPa.s. De viscositeit in mPa.s is sterk gedaald, maar als deze met een beker zou worden gemeten, zou er geen grote verandering kunnen worden gemeten, misschien 0,5-1 s. Bekers hebben niet de nauwkeurigheid om dergelijke problemen in de pers effectief tegen te gaan met de eenvoud en intuïtiviteit die het RPS-systeem onze operators in staat stelt.
De Nederlandse overheid eist dat we bijhouden en bewijzen hoeveel oplosmiddelemissies Maasmond heeft, waarvoor we emissiemetingen moeten doen en een oplosmiddelenbalansadministratie moeten voeren. We zien de laatste 2 jaar dat het verbruik van oplosmiddelen afneemt, vooral in 2020 zien we een enorme daling. In dat jaar werd de lamineermachine uitgerust met de viscositeitscontrole van Rheonics, wat resulteerde in een reductie van 21% ethylacetaat.
- Hoe gemakkelijk / moeilijk was het om de RPS in uw proces in gebruik te nemen? Wat zijn uw opmerkingen over de werking en bruikbaarheid van het systeem en de software? Vonden uw operators het gemakkelijk om het te begrijpen en eraan aan te passen?
Reactie:
Eigenlijk zijn de soft- en hardware plug and play.
Een belangrijk kenmerk van de Rheonics De SRV-viscometer is door het gemak van inline-integratie, wat lagere installatiekosten en inspanningen betekent. De SRV stelt geen eisen aan de wijze waarop deze wordt geïnstalleerd. Door de compacte afmetingen van de sensor neemt deze nauwelijks ruimte in beslag. Het genereert geen weerstand in de toevoerleiding en houdt de sensor bovendien altijd schoon. Trillingen veroorzaakt door pulsaties van pomp of machine hebben geen invloed op de sensor, wat een groot concurrentievoordeel is ten opzichte van andere vergelijkbare systemen. Zo moeten bij inkspec de sensoren geïsoleerd worden opgesteld, anders zijn trillingen (zelfs de sensoren beïnvloeden onderling de meting van elke individuele sensor) duidelijk zichtbaar bij de machines waar de inkspec-sensoren worden gebruikt. Dit neemt veel ruimte in beslag en maakt de installatie duur.
Vorig jaar hebben we een tweede RPS op de lamineermachine geïnstalleerd, de operators hadden alleen een korte uitleg nodig. Operators waren gewend in kop seconden te denken en eenmaal gewend aan de nieuwe unit weten ze precies wat ze doen. De viscositeit van 2-componentenlijmen is laag en kan door de hoge verdampingssnelheid van ethylacetaat zeer snel afwijken. De RPS InkSight software laat real-time zien wat de viscositeit is en de besturing zorgt voor compensatie voor de daadwerkelijke verdamping. Ook hier geldt dat voor verschillende ondergronden bepaalde viscositeiten voor de lijm gebruikt moeten worden en dat is nu perfect mogelijk. Wat me opviel is dat de lijmen nauwkeuriger worden voorbereid, tenminste de hoeveelheid ethylacetaat die aan het recept moet worden toegevoegd. De software geeft direct aan wanneer er te veel of te weinig wordt gedoseerd, wat voorheen niet het geval was. Ook als er tijdens het gebruik verse lijm aan de emmer wordt toegevoegd, ziet de operator wat er gebeurt en is het een uitdaging geworden om de lijm zo nauwkeurig mogelijk voor te bereiden.
- Is er iets over de technologie van de Rheonics oplossingen die u specifiek onder de aandacht wilt brengen? Hoe nauwkeurig en betrouwbaar presteren deze oplossingen in de pers in termen van uw procesdoelen?
Reactie:
Bij de aanschaf van nieuwe sensoren was mijn doel om nauwkeurige, compacte sensoren te hebben met weinig onderhoud. Qua nauwkeurigheid en betrouwbaarheid hebben de sensor en besturing onze verwachtingen / doelen overtroffen en geleid tot verbeteringen in kleurkwaliteit, efficiëntie en automatisering. Na verschillende oplossingen en technologieën voor printkwaliteitsbeheer te hebben geëvalueerd, geanalyseerd en getest, denk ik dat RPS een uiterst waardevolle toevoeging is aan onze pers - het maakt de controle van de belangrijkste variabele - 'inktviscositeit' supergemakkelijk, intuïtief en revolutionair in termen van nauwkeurigheid. Het zet een nieuwe maatstaf op het gebied van nauwkeurigheid. RPS is minstens 10-15 keer nauwkeuriger dan andere bestaande, toonaangevende inktviscositeitscontroles op de markt.
We printen op een vrij grote diversiteit aan folies en papier, waarbij verschillende viscositeiten gehanteerd moeten worden en met de ervaring die we nu hebben leert ons hoeveel een inkt verdund moet worden voor een bepaalde kleursterkte. Vaak gebruiken we een bepaalde die gebruikt wordt om op verschillende substraten te printen waarbij verschillende viscositeiten gebruikt moeten worden, bijvoorbeeld printen op bepaalde kleur op papier (hoge viscositeit is nodig) en dezelfde kleur wordt gebruikt voor printen op folie (relatief lage viscositeit ). We registreren voor elke bestelling, per kleur de viscositeit en welke rasterwalscilinder is gebruikt, zodat we precies weten welke viscositeit we moeten hanteren om de juiste kleurdichtheid te hebben, wat resulteert in een snellere insteltijd.
Een ander praktisch voordeel van RPS is dat er tijdens de viscositeitscontrole zeer kleine hoeveelheden oplosmiddel worden gedoseerd om de daadwerkelijke verdamping te compenseren. De meeste andere systemen vereisen tamelijk grote hoeveelheden inkt in het blik om viscositeitsschommelingen te vermijden die worden veroorzaakt door het doseren van grote hoeveelheden oplosmiddel met relatief lange perioden. Een grote hoeveelheid inkt zorgt voor stabilisatie van de viscositeit. Bij de RPS worden hoeveelheden tot 10 g gedoseerd. Om de inkt door het systeem te kunnen pompen hebben we minimaal 4 kg inkt nodig en soms hebben we nog maar 4.5 kg aan restinkt, terwijl de viscositeit de hele tijd stabiel is gebleven doordat er zeer kleine hoeveelheden worden gedoseerd. Dit betekent dat er minder inkt hoeft te worden voorbereid voor een bestelling en er minder restinkt ontstaat. Dit maakt de RPS ook uniek, omdat het kleine hoeveelheden inkt op een constante viscositeit houdt.
Bij handmatig gekalibreerde viscositeitscontroles zullen operators vaak geneigd zijn om een andere rasterwalscilinder met een ander volume te gebruiken of door vernis te gebruiken om de kleursterkte te beïnvloeden, wat resulteert in langere insteltijden.
Dit zorgt ervoor dat we daadwerkelijk een soort standaardisatie van drukkleuren op de verschillende ondergronden hebben bereikt. Dit scheelt veel tijd. Met handmatig gekalibreerde systemen is dit moeilijk te doen. Elke operator moet de discipline hebben om sensoren te kalibreren voordat de pers wordt ingesteld en heeft daar vaak niet de tijd voor.
- Levert de RPS volgens u een uniek voorstel aan de drukkerijen? Denk je Rheonics met de RPS impact kan maken in de flexodrukindustrie?
Reactie:
Ten eerste is het de enige sensor die gekalibreerd is bij de leverancier en daarna nooit meer gekalibreerd hoeft te worden. Met deze sensor is het mogelijk om viscositeitswaarden op te slaan, waardoor automatisering mogelijk is. De belangrijkste variabele wordt gemeten met sensoren die niet voor elk instelpunt handmatig gekalibreerd hoeven te worden, waardoor door de operator veroorzaakte fouten worden geëlimineerd.
Een goede vergelijking van de Rheonics sensoren met sensoren die op de markt verkrijgbaar zijn, zijn een laserafstandsmeter en het bepalen van de diepte van een put door een steen te laten vallen en de tijd te meten die nodig is voordat deze de bodem raakt. Met steen en klok heeft de put een diepte van 21,3 seconden, voor het geval de put niet diep genoeg is zegt de man met de klok “graaf nog eens 0,5 seconde” of in het geval van Rheonicsgraaf met een nauwkeurigheid van enkele mm.
Als ik met de verkoper/technicus van de inkt spreek en er zijn problemen met een klant, komt dat vrijwel in alle gevallen doordat de viscositeit van de inkt veel stroperig is. Zelfs bij collega's wanneer er tijdens het printen een fout wordt ontdekt, is het meestal dat er te veel oplosmiddel in de inkt wordt gedoseerd, waardoor de kleur afneemt.oring sterkte.
Een van de redenen waarom iedereen accepteert dat viscositeit wordt uitgedrukt in seconden, is dat er geen "betrouwbare, reproduceerbare" sensoren waren die in de juiste eenheid meten, dus er was geen alternatief.
Ik geloof dat het RPS-systeem de veiligheidsnormen en automatiseringsmogelijkheden in de pers naar een hoger niveau tilt en een nieuwe maatstaf zet voor drukkerijen op het gebied van kwaliteit, winstgevendheid, kleurprecisie en -nauwkeurigheid, beheer van het inkt- en oplosmiddelverbruik, de kennis en controle van operators en de impact op het milieu. Ik ben er zeker van dat het een stempel zal drukken op de flexodrukindustrie; het brengt de meest cruciale drukvariabele, namelijk de inktviscositeit, binnen handbereik van de printers. Rheonics RPS- en SRV-sensorsystemen bieden de volgende belangrijke voordelen en een uniek voorstel:
Technische voordelen: Persautomatisering, kwaliteitscontrole, efficiëntie, nauwkeurigheid en milieu
- Veel strakkere, nauwkeurigere (minstens 10-15 keer) controle van de inktkwaliteit in vergelijking met andere gelijkwaardige systemen op de markt.
- Snellere insteltijd en nauwkeurige kleurdichtheid - ondersteund door ervaring en sensorherhaalbaarheid, laadtaakconfiguratiefuncties van software
- Temperatuurgecompenseerde viscositeit: minder zorgen over seizoensschommelingen of enige factor die de temperatuur (en dus de viscositeit) kan beïnvloeden
- Compensatie voor verdamping: strakke controle en 'fijne resolutie' van toevoeging van oplosmiddelen in kleine stappen - dit alles leidt tot besparingen van oplosmiddel en inkt
- Vermindert insteltijd en insteluitval - operators kunnen een eerder geladen taak opnieuw uitvoeren met de functies 'Opdracht opslaan' en 'Opdracht laden', wat de verspilling vermindert
- Effectieve foutanalyse en probleemoplossing - de meeste problemen bij het afdrukken met betrekking tot kleur en kwaliteit worden toegeschreven aan viscositeitsproblemen. De gegevens van de sensoren en het RPS-systeem zorgen voor een efficiënte foutdetectie, uitgebreide analyse van de hoofdoorzaak en effectieve corrigerende maatregelen op een eenvoudige en intuïtieve manier.
- Minder uitstoot van oplosmiddelen en minder afval en verspilling in vergelijking met handmatige hantering en instellingen.
- Kortere droogtijd en besparingen door verminderde behoefte aan terugwinning van oplosmiddelen dankzij optimaal gebruik van oplosmiddel in inkt.
Installatie en bruikbaarheid
- Compact formaat: kleine voetafdruk in de pers, niet beïnvloed door omgeving - trillingen enz. Andere soortgelijke systemen vereisen een aanzienlijke installatie-inspanning en voetafdruk in de pers. We hoefden de sensor alleen rechtstreeks in de inktslang te installeren, met een standaard off ”T-stuk.
- Software is intuïtief, gebruiksvriendelijk en waardevol. Bovendien helpt het om de knowhow van operators over viscositeit en kleursterkte-correlaties te ondersteunen - ze hebben nu een slimme manier om kennis te begrijpen, te experimenteren om de kennis over het gedrag van inkten te vergroten - nuttig bij huidige en toekomstige banen. De software is gemaakt in samenwerking met operators, wat heeft geresulteerd in een zeer gebruiksvriendelijke interface. Af en toe wil een operator zien hoe de viscositeit zich heeft gedragen tijdens de productie van een order, hoe stabiel deze was.
Winstgevendheid
- Besparing op het verbruik van oplosmiddelen en inkt (ook het bijhouden van het verbruik van oplosmiddelen): strengere controle leidt tot een lager verbruik van oplosmiddelen en inkt dankzij het innovatieve algoritme + systeem superioriteit.
- Kortere insteltijden leiden tot productiviteitsverbetering en mogelijkheden om meer afdruktaken in dezelfde tijd af te werken.
- Mogelijkheid om banen van hogere kwaliteit en hogere marges (dE <2) aan te nemen, wat de winstgevendheid verhoogt en een concurrentievoordeel oplevert
Enkele afbeeldingen van het RPS InkSight-systeem
- Rheonics SmartView-console geïntegreerd in drukmachines
- Enkele foto's die de inline installatie van de SRV-viscositeitsmeters in de pers laten zien
- Standalone schakelkast
Alles Rheonics producten zijn ontworpen om bestand te zijn tegen de zwaarste procesomgevingen, hoge temperaturen, hoge schokken, trillingen, schuurmiddelen en chemicaliën.
Gerelateerde artikelen
FTA Flexo Magazine biedt een Rheonics gebruikerscasestudy – “Viscositeitsstandaardisatie: één printerbenadering”
Op flexografisch drukwerk gericht tijdschrift - Flexo (https://www.flexography.org/flexo-magazine/) publiceert een diepgaand artikel waarin de Rheonics SRV-viscometers en de RPS InkSight Multi-Station Ink Control-oplossing op een klantlocatie in Nederland. Zoek de link naar de publicatie.
Viscositeitsstandaardisatie bij flexografisch afdrukken
In de geschiedenis van ons bedrijf hebben we elk type viscositeitssensor toegepast: rotatie, vallende bal, vallende zuiger en akoestische golf. De overeenkomst tussen deze sensoren is dat ze allemaal gekalibreerd zijn met een beker, in ons geval de DIN-beker met een 4 mm uitloop. Op zich werkte dit goed en bij gebrek aan een beter alternatief ...